Manufacturing Asset Management Dashboard Case Study
Overview

This case study focuses on the development of an Asset Management Dashboard for the manufacturing sector, showcasing a collaborative effort between the development partner and a Fortune 500 company. The project’s primary goal was to enhance manufacturing processes through data management solutions.
Client Background: The client, a multinational corporation headquartered in Switzerland, operates in the fields of robotics, heavy electrical equipment, automation, and technology. They sought to leverage data management and data solutions to optimize manufacturing processes and improve their competitive edge.
Project Challenges
The project began with the client’s desire to employ effective data management and data solutions in the manufacturing sector. They aimed to track and manage manufacturing plants by utilizing big data and IoT technologies.
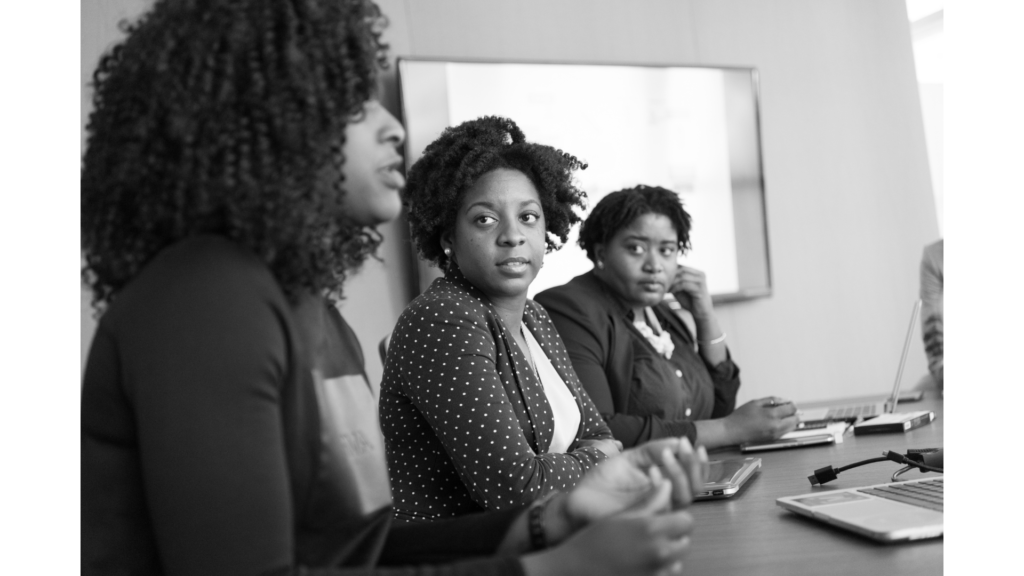
Project Phases:
01 Strategy
The project followed a Time and Material engagement model for 11 months.
02 Analysis Planning
React JS with MobX was chosen as the primary technology stack for the project, with a focus on Frontend development.
03 UI/UX
User familiarity with technology was considered during the design process for both web and mobile applications.
04 Development
The development phase included creating features such as a homepage with summaries from widgets, widget tabs, logs, charts, and labels for an enhanced user experience.
05 Testing
Rigorous User Acceptance Testing (UAT) was conducted at every stage of development to ensure the product’s quality met expectations.
06 Delivery
After 11 months of continuous effort, the collaboration successfully produced an asset management dashboard, promising to revolutionize manufacturing processes.
Final Impression
The client expressed satisfaction with the project’s quality, professionalism, and punctuality of the team members. The development partner has been entrusted with additional projects by the client, highlighting the strength of their collaboration. Both parties look forward to maintaining a long-term relationship and pursuing future collaborations.
This case study illustrates how effective data management and data solutions can revolutionize manufacturing processes, emphasizing the importance of strategic planning, technology selection, development, testing, and successful collaboration to achieve project goals.
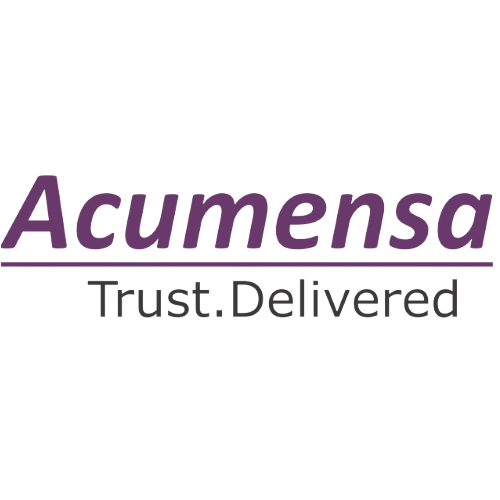
Useful Links
- 225 St Pauls Ave Jersey City, NJ 07306 USA
- info@acumensa.co
- +1 917 934 3024
- Salarpuria Symbiosis - Ground Floor, Begur Hobli, Bannerghatta Main Rd Bengaluru 560076
- info@acumensa.co
- +91-7406447843
Our Resources
©2023 Aumensa Technologies All Rights Reserved.